Fitness
Perfecting the art of manufacturing fitness equipment
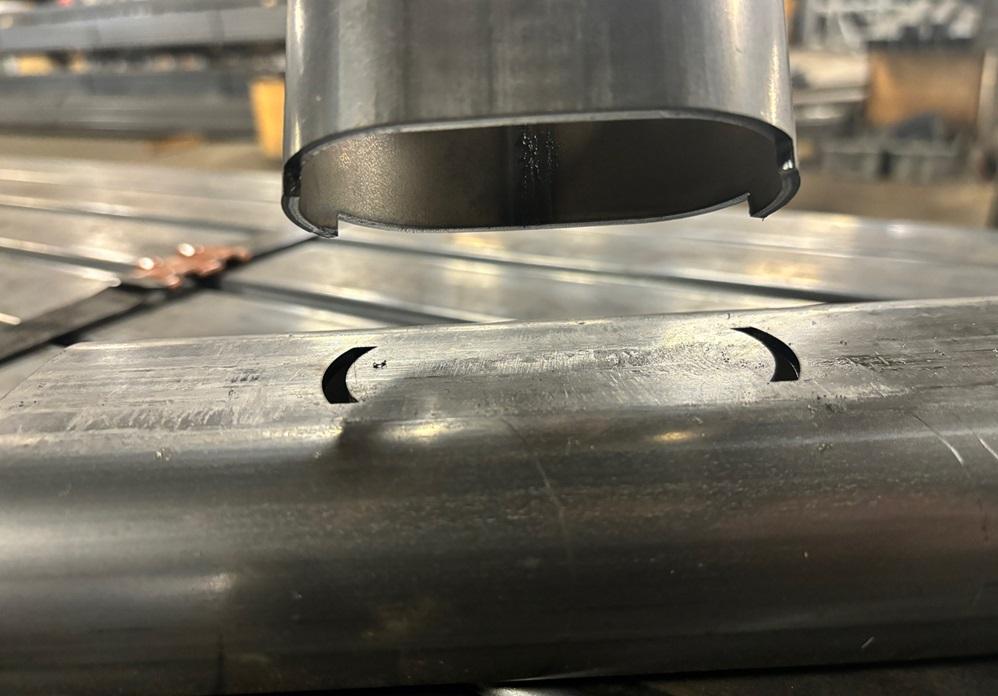
With the LT Fiber system, Atlantic Strength can cut notches in its tubes so they can be assembled like a puzzle, eliminating the need to measure the parts. Images: Atlantis Strength
For nearly 40 years, Atlantis Strength has been a leading manufacturer of commercial-grade fitness equipment in Canada. But remaining a leader in such a competitive and fickle field as the fitness industry requires constant fine-tuning and changes to improve both the design and manufacture of its nearly 300 SKUs of mostly steel weight-training products.
That’s why in 2016, the company began to search for a more innovative and reliable way to meet its growing metal cutting needs in an effort both to reduce its reliance on outsourcing for laser cutting and to end its arduous use of a hybrid machine that required manual cutting.
“Almost all of our products are designed and built with steel in-house, and demand is booming—and has been for years,” said Jordan Sansoucy, Atlantis Strength CEO and son of the company’s founder, Raymond Sansoucy. “It got to the point where we wanted to add laser cutting to our in-house abilities in order to have better control over the cost and inventory of the components we make and use to build our equipment.”
Enter BLM GROUP, a manufacturer of high-precision laser cutting and sawing machines and CNC bending and end forming machines.
After several visits to Atlantis Strength’s two-building plant and headquarters in Laval, Que., and many meetings and discussions between BLM GROUP sales representatives for Eastern Canada and the fitness equipment company’s production team, Atlantis inked a deal to buy BLM GROUP’s LT Fiber in 2017.
Enhanced Functionality With Fiber Laser Cutting
One in a family of laser cutting systems in which the beam is generated directly inside the optic fiber itself—as opposed to systems that generate the laser beam externally and then introduce and transport the beam via the optic fiber—the LT Fiber is designed to help maximize both the performance and results of fiber laser technology.
The 3D system offers high beam quality, a fast cutting speed-to-laser power ratio, the ability to process highly reflective materials, and reduced electric energy consumption. It also features automatic changeovers of jobs in less than two minutes, with the CNC adjustment settings at the push of a button. Tubes are measured in the preload position and supported through to completion to help ensure maximum cut quality and precision.
The adaptability of the machine and its programming software also allows for the processing of special sections and profiles in a fully automated working cycle. Its use of gas to cut helps keep maintenance costs down.
Installed and in operation at Atlantis Strength since early 2020, the laser system has more than lived up to expectations.
“It’s given us design possibilities that we weren’t even aware of—and that we’re still exploring and mastering,” said Andre Luciano, the company’s director of operations.
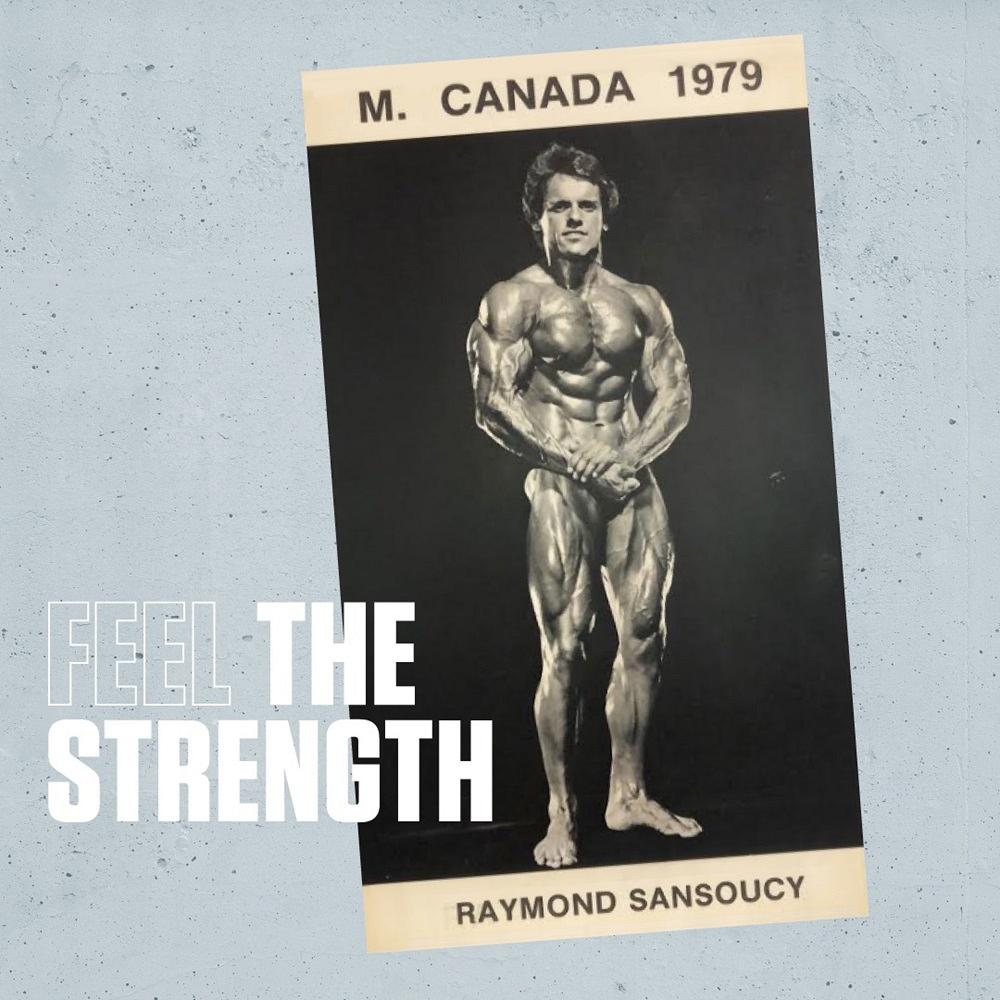
A bodybuilder who won a Mr. Canada title in 1979, Atlantis Strength founder Raymond Sansoucy used the ideas and inspiration he got visiting gyms to start designing and building strength equipment with mostly welded frames, heavier gauges of steel, and higher resistance.
According to Luciano, the system notably allows numbers to be cut on the steel components that go into its gym equipment—a welcome change and more durable alternative to the numbered stickers that used to be applied to those parts manually.
“We can also cut notches in tubes now,” he said. “That makes them easier to assemble, like a puzzle, instead of having to measure them like we did before.”
Expanded Capabilities With Tube Bending
Thanks to the successful integration and use of the LT Fiber system, Sansoucy said his company again turned to BLM GROUP when it decided to further strengthen its in-house production capabilities by acquiring an automated tube bending machine.
“We were at the mercy of one company in Quebec that could do what we needed,” he said. “We’d send them batches of 40 tubes and then stockpile them when they came back and use them when they were needed. But it cost a lot of money and took up a lot of space.”
He said having its own tube bender would bolster his company’s just-in-time inventory needs and help meet the insatiable market demand for high-quality, made-to-order fitness equipment like Atlantis makes.
“We have 35 weeks’ lead time with no time to build and keep inventory,” said Sansoucy. “The more stages of the production process we can control, the better.”
The company eventually settled on BLM GROUP’s Elect 102 tube bender. Fully automated and configurable, the machine is designed to bend tubes with standard or special cross sections; end formed tubes; tubes with minimal straight between bends; and tubes of various materials, including noble, stiff, and soft metals.
Simple enough to be operated by inexperienced operators, the bender can be equipped with up to eight bending toolsets and is available in different sizes for tubes up to 150 mm dia. In addition to providing speed, efficiency, and minimum ovalization even on extremely tight bends, the system can perform fixed- and variable-radius bends with zero scrap.
“It’s won us time and space,” said Luciano. “We use it every day. And we’re still adjusting and doing different programs in order to maximize the machine’s use and potential.”
New and Changing Opportunities
The company uses the machine to bend the tubes needed to make gym equipment from plate-loaded machines, weightlifting platforms, and multistations to racks, rigs, and benches. It sells these products to professional teams, schools, and gyms, as well as to private training and high-end residential facilities through 40-plus dealers in more than 65 countries around the world.
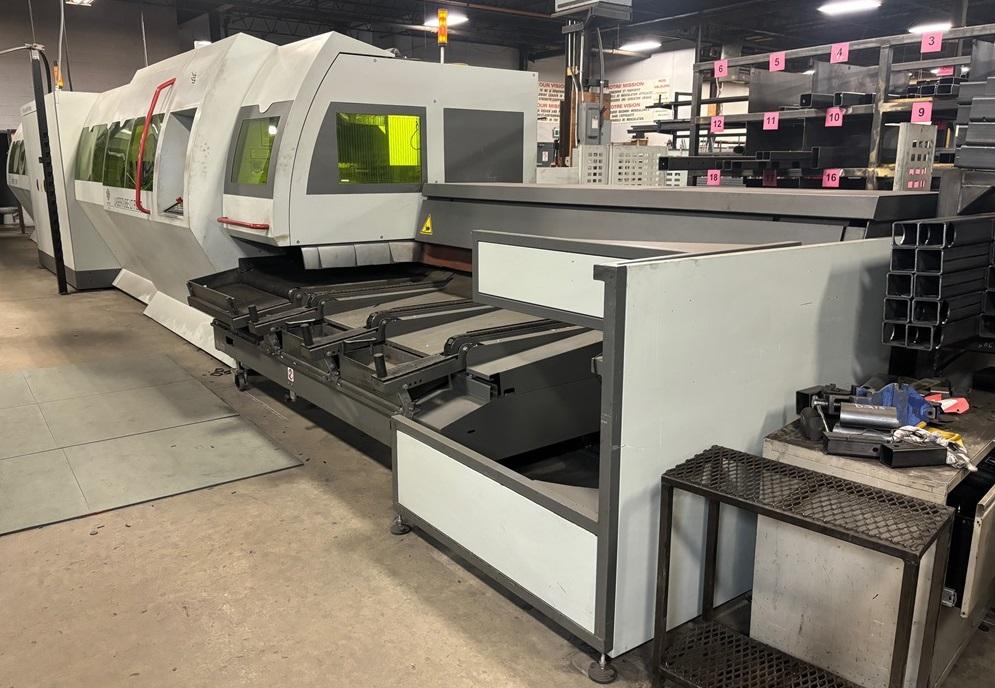
The LT Fiber system has offered the company new design possibilities that it is currently exploring and mastering.
Sansoucy said he and his production team will continue looking for ways to streamline and improve operations. That may one day include the addition of new machines like robot welding cells and laser cleaning machines to remove rust from various metals without damaging them.
“Our focus is on controlling costs and improving manufacturing with new programs and systems,” said Sansoucy. “That way, we can continue to grow and to capitalize on new opportunities in emerging markets like Asia.”
He said the design and quality of modern gym equipment—much like the exercise methods and dietary regimens that trainers, athletes, and everyday people use to achieve their bodybuilding, strength, and fitness goals—have evolved greatly since his father started making his own equipment in the early 1980s.
A bodybuilder who won a Mr. Canada title in 1979, Raymond Sansoucy used the ideas and inspiration he got visiting and working out at gyms and health clubs across the U.S. and Canada to start designing and building strength equipment with mostly welded frames, heavier gauges of steel, and higher resistance levels—the same cornerstones used to build Atlantis products today.
“A lot of what was available in the old days was fine for lighter applications, but it would not survive heavy use or was not heavy enough to use,” Raymond Sansoucy wrote in a history about the company on its website. “I wanted to make equipment that stronger people could work out on and not have to fix every week.”
Raymond faced many challenges in those early years as he juggled school, family, and his startup manufacturing business.
“It was very difficult,” he continued. “We had to improvise because components were scarce and everything was new. I was also running my gym and doing my degree at night, so sometimes I had to finish pads at 4 a.m. so I could deliver that day.”
As the business grew, mostly due to demand from across Canada and the U.S., so too did the need for manufacturing space. After several moves, Atlantis settled in its current location in 1998.
The company now has roughly 100 employees, most of them involved in the design and production of gym equipment that meets the ever-changing trends and needs of the fitness industry.
Though his son Jordan is now responsible for the company’s daily operations, Raymond, now 68, is in charge of research and development of new products.
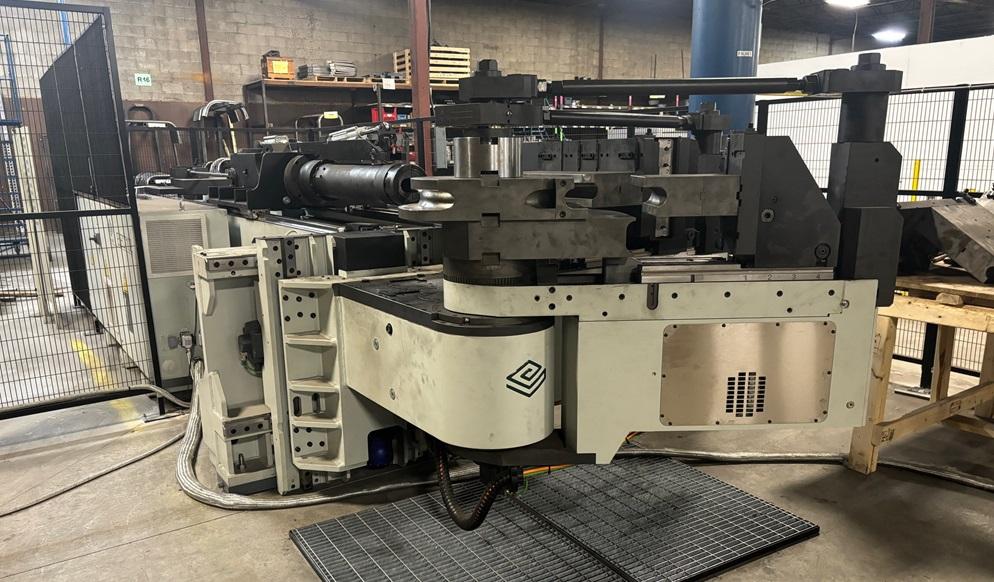
The BLM Elect 102 tube bender has won Atlantis Strength both time and space. The company uses it every day, adjusting and tweaking different programs to maximize the machine’s use and potential.
“Today’s facilities must accommodate a much broader membership than ever before, and we’re sensitive to the new demands being placed on our customers,” wrote Raymond. “We have been perfecting strength equipment for over 40 years, and I have no plans to stop anytime soon.”
Jordan, who worked summers in the family business growing up and joined the firm in 2019 after graduating from Montreal’s Polytechnique with a degree in chemical engineering, said his efforts as CEO are focused on finding ways to keep the company lean, mean, and cutting edge.
“I grew up watching my father run Atlantis Strength and regularly visited gyms with him whenever we traveled,” he said. “That allowed me to keep up with day-to-day operations of both the business and the fitness industry.”
His focus is on finding ways to make the company run more efficiently and to help build the Atlantis Strength brand.
“We’re all about helping people push beyond their limits and become better, both physically and mentally,” he said. “We design and make every piece of equipment with the user in mind and with the best materials possible. And to make quality products, we rely on quality people, parts, and partners.”
Editor’s Note: This feature originally appeared in the January 2024 issue of Canadian Fabricating & Welding.